How Do You Optimize Logistics Cost?
May 26, 2022 •Deyman Doolittle
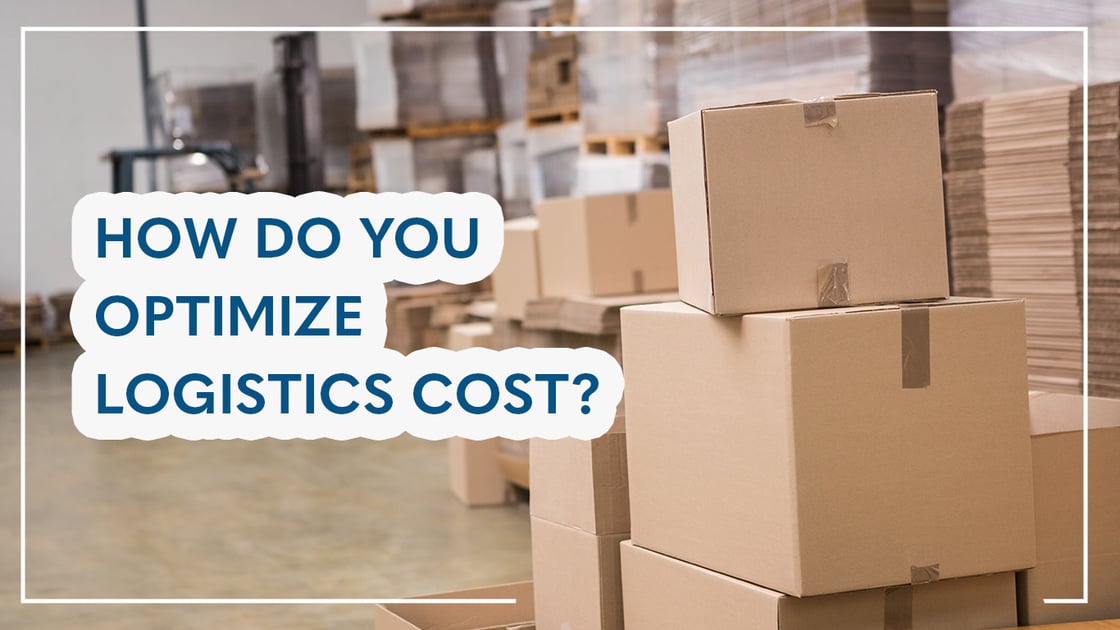
For businesses operating anywhere along the supply chain, minimizing costs is essential to maintaining profitability. Yet according to the Wall Street Journal, total shipping costs have increased over 23% since 2020, and there is no sign of that rate slowing down. With such a steep increase in shipping costs, businesses must creatively and efficiently cut costs elsewhere, including logistics.
One of the many ways to optimize logistics costs is by gleaning insights from a regular parcel invoice audit. However, logistics and shipping optimization doesn’t stop there. In this blog, we’ll explore actionable ways to reduce logistics costs.
What Is Logistics Cost Optimization?
Before discussing logistics cost optimization, we should take a step back and define logistics optimization as an umbrella term. Logistics optimization refers to the best practices and strategies that help to ensure steps along the entire supply chain are organized and efficient. For companies, logistics optimization can refer to strategies that improve both inbound and outbound processes.
Logistics cost optimization, then, looks at specific strategies and practices to help companies minimize their overall logistics spending. Reducing costs while still maintaining a high level of quality along the supply chain is key. Types of logistics costs that could be optimized may include:
- Shipping and transportation
- Warehouse costs, including rent
- Inventory storage and management
- Packaging supply costs
- Equipment costs
- Labor and employee benefits
How Can Logistical Costs Be Reduced?
There are several ways businesses can realize reduced logistics costs like those discussed above. Of course, companies may not need to alter or improve in each of these areas, but analyzing all of them can provide a high-level, holistic overview to work from. Businesses can use the following strategies to begin looking at how to reduce their logistics cost.
Develop Goals
Before beginning any logistics optimization project, companies should determine what goals they would like to accomplish. To achieve the best results, goals should be both specific and measurable. For example, is there a certain percentage of logistics costs that need to be cut? Are there specific areas where costs are running higher than usual?
Perform Audits
Once goals have been developed, companies will likely need to gather and analyze data. This might include auditing certain processes or spend to identify areas of improvement. At ShipSigma, we specialize in parcel invoice audits. Our AI-powered platform automatically scans weekly carrier invoices, performs a 50+ point audit, and automatically files claims to save you money.
Review Contracts
Reviewing your shipping and logistics contracts to potentially negotiate a better deal can provide significant savings. For example, could you order more shipping materials (like boxes) at a time to receive a higher discount? Are there better rates you could receive from your carrier? ShipSigma can help your company cut parcel shipment costs with carrier contract negotiations.
Eliminate Errors
One of the simplest ways to cut costs is by eliminating errors. A parcel invoice audit is an excellent way for logistics leaders to identify errors that can be corrected. For example, an audit may reveal that shipments are incorrectly being flagged as residential or that there has been an uptick in address correction charges. Once these issues have been identified, leaders can work with teams to improve data and processes to minimize unexpected fees and charges.
Automate Processes
Automating basic data collection and integration processes can help companies in several ways. First, automating processes can cut labor costs, freeing up your employees for other types of work. Second, automating data processing eliminates the possibility of human error, which can lead to a decrease in carrier fees and charges associated with incorrect data.
Maintain Equipment
For companies that use any machinery, a preventative maintenance schedule can help limit costs associated with downtime and costly reactive repairs. If your forklift dies, for example, operations will be significantly impacted until it can be fixed.
Consolidate Shipments
There are many options for shipment consolidation, which can lead to tremendous cost savings. Teams may work to align inbound and outbound shipments with their shipping companies. Options for less-than-truckload (LTL) versus full load shipping (FTL) should also be explored.
Improve Communication and Training
Before enacting any changes to processes or procedures, it is critical that all employees have been fully informed and trained on any new knowledge or skills they’ll need. Prioritizing communication and training can help ensure that your business’s new practices are implemented quickly and effectively so you can start seeing cost savings sooner.
ShipSigma: Helping High-Volume Shipping Businesses Save
Optimizing every part of your business can lead to higher profitability, increased customer satisfaction, and improved efficiency. At ShipSigma, our goal is to help companies save money on their shipping and logistics spending. ShipSigma provides high-volume shipping businesses with parcel invoice audits, automatic billing error refunds, carrier contract negotiations, and shipping insights & analytics to cut shipping costs by an average of 25%.
Ready to start saving? Try it free today.